Lots of small changes - lead to a fully assembled half!
- YoyoTeam JAHA
- Nov 10, 2020
- 2 min read
After fighting with the newly thickened outer ring of the metal part and having issues with a few of the ejector pin holes, we decided to remachine that mold on Friday. Now the force from the ejector pins is directly on the base of the part so it is much easier to eject and will allow for much faster manufacturing time for that part (we were prying every part out of the molds before!) We also decided to remove the ramp angle that was on the metal ring to help with ejecting after we saw that it ejected well with the new ejector pin placement. This is because the snap fit too easily popped off of the bottom of the top outer diameter. We decided that the tradeoff of having a little of the ejector pin marks visible was worth the faster ejection time!

In addition, we also did some work on the bottom of the top. We played with the BOY settings until we were able to have minimal sinking and no flash. This was mostly dictated by the shot size and pack time. After making a few of these parts, we realized that there was an offset between the 2 molds that was quite noticeable. So we decided to remachine the cavity of the part in order to fix that misalignment. We are doing that in lab today - fingers crossed this is the last remachine we'll have to do!

Moving forward we plan to injection mold the metal part and the newly aligned bottom of the top in lab today and make sure they fit.
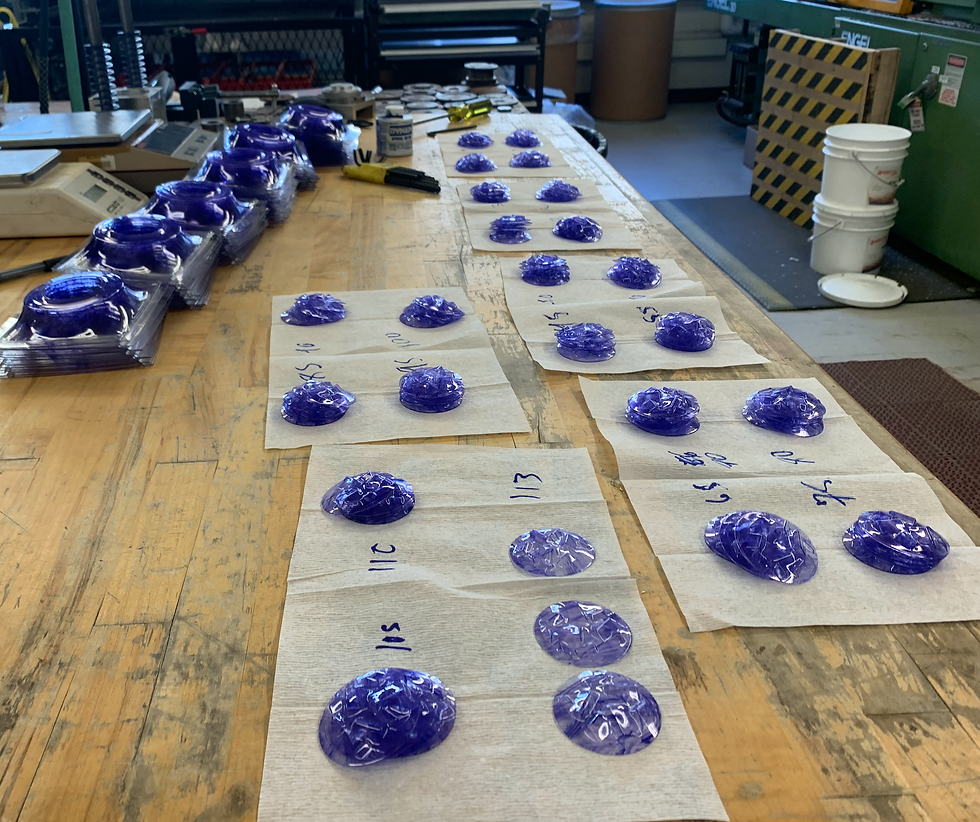
In addition, we have all of our thermoform parts done and cut out on the die! They were colored blue Steel Blue layout fluid.
Comments